In the world of electrical systems and maintenance, a proactive approach can make all the difference in preventing unforeseen fires, outages, and injuries. One program that has been at the forefront of proactive electrical maintenance is Miller Electric’s TEGG service.
We sat down with Brian McAndrew, Miller Electric Electrical Risk Consultant with extensive experience in TEGG projects, to learn more about the program and how it has made a significant impact on client facilities.
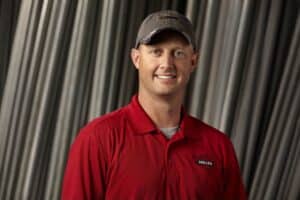
Brian McAndrew, Electrical Risk Consultant
The Power of TEGG
TEGG is more than just a program; it’s a proactive approach to electrical maintenance and one that emphasizes electrical safety. Brian describes it as a way to shift from a reactive mindset to a proactive one. The goal is to detect anomalies, code violations, safety issues, and potential electrical hazards before they lead to costly emergencies.
Recent TEGG Projects: Unveiling Hidden Dangers
One of the key benefits of TEGG is its ability to uncover hidden dangers that would otherwise go unnoticed. Brian shares some recent projects that highlight the program’s value.
Transformer Surprises
During routine scans at a client’s facility, the TEGG team stumbled upon a startling discovery. Transformers, crucial components of electrical systems, were found to contain paper debris inside.
Left unattended, this could have resulted in a fire if the transformers overheated. Brian emphasizes that such issues often remain hidden until preventive maintenance is performed, making regular scans crucial. “We recommend maintenance every year,” he advises.
Circuit Breaker Catastrophe
In another instance, a circuit breaker had failed so severely that it melted a portion of the breaker body, causing the body of adjacent breakers to melt from excessive heat.
Remarkably, the damaged breakers were still functioning, but their failure was imminent. Without the TEGG scan, this dangerous situation would have gone unnoticed until a catastrophic failure occurred.
The Standard TEGG Program
TEGG offers a range of services tailored to meet clients’ specific needs. One of the most popular options is the standard TEGG program. Brian explains that the program’s structure has evolved to adapt to clients’ requirements. However, it typically includes the following components:
- Infrared Scanning: A comprehensive infrared scanning process is conducted, focusing on electrical equipment. This scan identifies anomalies, overheating issues, and potential electrical hazards.
- Detailed Reporting: Every piece of equipment scanned receives an itemized report. This report includes images, amperage and voltage readings, and itemized descriptions. Clients can choose between deficiency-only reports or complete reports, depending on their preferences.
- Online Portal: TEGG provides an online portal where clients can access their accounts, view past scan results, and review reports digitally. This digital approach reduces the need for printing large binders of documentation, conserving resources, and costs.
Proactive Service: A Game Changer
The proactive nature of TEGG’s services can have a profound impact on a client’s operations. Brian emphasizes the significance of proactive maintenance, particularly in scheduling shutdowns and avoiding costly emergency situations. Clients can plan maintenance on their terms, minimizing disruptions and financial losses.
Additionally, the online portal offered by TEGG simplifies record-keeping and access to historical data. Clients can conveniently access their scan results from previous years, aiding in audits and insurance rebate applications.
Arc Flash Analysis: Another Critical Safety Offering
Another proactive service and critical electrical safety service Miller Electric offers is Arc Flash analysis. As we’ve written about elsewhere, protecting workers and facilities from arc flash danger is critical. An arc flash analysis determines the incident energy a worker may be exposed to and shows how to protect workers from arc flash incidents and other electrical hazards.
As part of an arc flash analysis, Miller Electric provides:
- PPE labels on each piece of equipment that tell qualified personnel exactly what level of PPE is required when working on energized equipment
- One-line diagram of a facility
- Fault currents at each location, describing where ‘electrical bombs’ (i.e., electrical equipment that is over-duty and cannot withstand incident energy) are in a facility
- Mis-coordination of protective devices
An arc flash analysis puts customers in compliance with NFPA 70B and NFPA 70E electrical codes. Based on the assessment, customers know exactly what safety measures and PPE is needed to mitigate risks and protect workers and facilities from danger.
Looking to the Future
Brian reflects on his experience with TEGG over the past decade, noting how the program has evolved and gained recognition.
“Over the years, the idea of preventative maintenance through the TEGG program has really caught on,” he says.
In recent years, Brian has worked to bring TEGG services to existing clients who were previously unaware of the program’s full scope. He highlights the flexibility of TEGG in adapting to clients’ specific needs, including custom reporting to suit individual requirements.
TEGG and Safety
Lastly, Brian notes that some insurance agencies offer rebate discounts on insurance premiums for clients who undergo infrared scans. This not only underscores the safety benefits of the program but also highlights the potential cost savings associated with proactive electrical maintenance.
Miller Electric’s proactive approach to electrical maintenance has proven its worth time and again by uncovering hidden dangers and preventing costly emergencies.
As technology continues to evolve, so too will Miller Electric’s proactive, preventative maintenance services, ensuring that clients stay one step ahead of electrical hazards, and enjoy the peace of mind that comes with a safer and more efficient electrical infrastructure.